Air-Cooled VW Product Catalogues
VW Split Screen Van
VW Bay Window Van
VW Beetle
VW Type 3
VW Thing / Trekker
VW Karmann-Ghia
VW Engines T1+T4
VW Electrical
IGNITION SYSTEMS
TOOLS
Other (Non VW) Product Catalogues
Air Cooled Porsche
Rover V8 Parts
Ford Kits
BMC Era Car Parts
Land Rover Kits
|
Criteria For The Correct Selection Of Strength Grade For Seat Belt Bolt
US Federal Law On Seat Belt Hardware
  |
US Dept ofTransportation : Federal Motor Carrier Safety Administration
From : http://www.fmcsa.dot.gov/rules-regulations/administration/fmcsr/fmcsrruletext.aspx?section=571.209
(S4.1)(f) Attachment hardware. A seat belt assembly shall include all hardware necessary for installation in a motor vehicle in accordance with Society of Automotive Engineers Recommended Practice J800c, “Motor Vehicle Seat Belt Installation,” November 1973. However, seat belt assemblies designed for installation in motor vehicles equipped with seat belt assembly anchorages that do not require anchorage nuts, plates, or washers, need not have such hardware, but shall have 7/16-20 UNF-2A or 1/2-13UNC-2A attachment bolts or equivalent metric hardware. The hardware shall be designed to prevent attachment bolts and other parts from becoming disengaged from the vehicle while in service. Reinforcing plates or washers furnished for universal floor, installations shall be of steel, free from burrs and sharp edges on the peripheral edges adjacent to the vehicle, at least 1.5 mm in thickness and at least 2580 mm 2 in projected area. The distance between any edge of the plate and the edge of the bolt hole shall be at least 15 mm. Any corner shall be rounded to a radius of not less than 6 mm or cut so that no corner angle is less than 135° and no side is less than 6 mm in length.
(S4.2)(b) Breaking strength. The webbing in a seat belt assembly shall have not less than the following breaking strength when tested by the procedures specified in S5.1(b): Type 1 seat belt assembly- 26,689 N; Type 2 seat belt assembly- 22,241 N for webbing in pelvic restraint and 17,793 N for webbing in upper torso restraint.
(S4.3)(c) Attachment hardware. (1) Eye bolts, shoulder bolts, or other bolt used to secure the pelvic restraint of seat belt assembly to a motor vehicle shall withstand a force of 40,034 N when tested by the procedure specified in S5.2(c)(1), except that attachment bolts of a seat belt assembly designed for installation in specific models of motor vehicles in which the ends of two or more seat belt assemblies cannot be attached to the vehicle by a single bolt shall have breaking strength of not less than 22,241 N.
(S5.2)(c) Attachment hardware. (1) Attachment bolts used to secure the pelvic restraint of a seat belt assembly to a motor vehicle shall be tested in a manner similar to that shown in Figure 3. The load shall be applied at an angle of 45° to the axis of the bolt through attachment hardware from the seat belt assembly, or through a special fixture which simulates the loading applied by the attachment hardware. The attachment hardware or simulated fixture shall be fastened by the bolt to the anchorage shown in Figure 3, which has a standard 7/16 -20UNF-2B or 1/2-UNF-2B or metric equivalent threaded hole in a hardened steel plate at least 10 mm in thickness. The bolt shall be installed with two full threads exposed from the fully seated position. The appropriate force required by S4.3(c) shall be applied. A bolt from each of three seat belt assemblies shall be tested.
|
Basic Interpretation Of US Law
  |
First of all we need to put the Seat-Belt Bolt loading into perspective by calculating the G-Force deceleration implied by the requirement. If we assume a hefty 250lb+ individual is being restrained by the Seat-Belt :
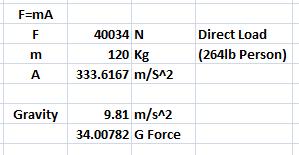
So we can see that we have a 34G loading (this figure would rise for a smaller weight of restrained occupent) - which for all intents and purposes is the loading induced by a severe crash.! This is the equivalent of going from approx. 800mph to zero in a single second.!! Or driving into a brick wall at 40mph (arresting to zero in 0.05 of a second).!
FURTHER : It should be remembered that most Seat-Belts are 3-Point types - so there would be 3 bolts/nuts taking the load of the 'shock' deceleration - the above calculation is assuming ALL of the occupents decelerative Mass is focused onto the one bolt.
For the purpose of the making the following calculations we have to resolve the input force (at 45 degrees application angle) into a shear loading and a tensile loading component.
|
Shear Calculation on 304 (A2-70) Bolt
  |
Calculations / Unit Conversions from Imperial to Metric not shown for brevity.
|
Thread Loading Calculation on 304 (A2-70) Bolt
  |
First of all let us consider the basic UNF threadform :
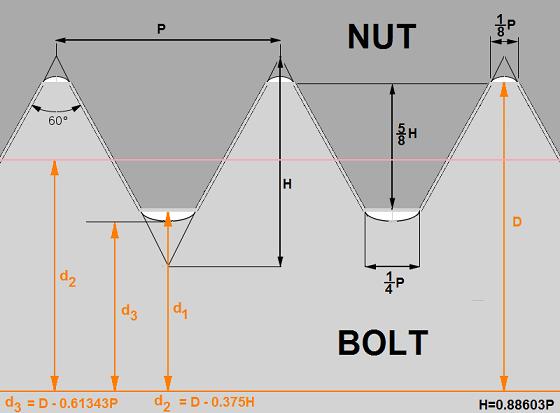
First Pass : consider the traditional STRESS AREA of the thread under TENSILE loading (As) :

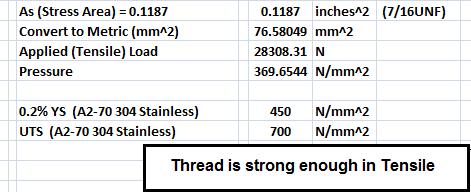
Second Pass : consider the first Turn of Thread Loading ONLY :
There is a widespread assumption that each turn of thread in a nut and bolt will take and hold an equal share of the load applied. Therefore, the assumption goes - to handle higher loads one simply increases the length of engaged turns of thread.
In reality it is found that the first turn of engaged thread presented to the load will be subjected to the highest load, with each subsequant turn of thread handling proportionally less and less, with their being no net advantage to engaging over one (1) nominal shank diameter worths of thread (approximatley six (6) turns). This extends out to 1.5 shank diameters of threading in Aluminium. This is envisaged diagramatically below :
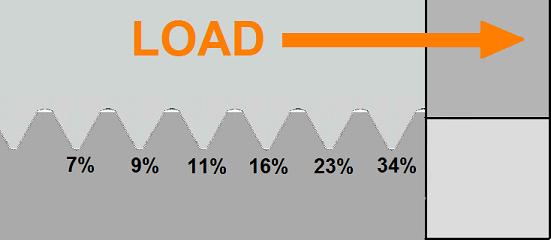
So what we need to do now is calculate the surface area of the loaded section of a single thread - we can do this using the data provided above as its simply the surface area of two cones (one subtracted from another). We can also resolve the Force so it is presenting itself perpendicular to the loaded face of the material (both full Force AND resolved Force can have pressure loading calculations - that part is easy inside a spreadsheet.!
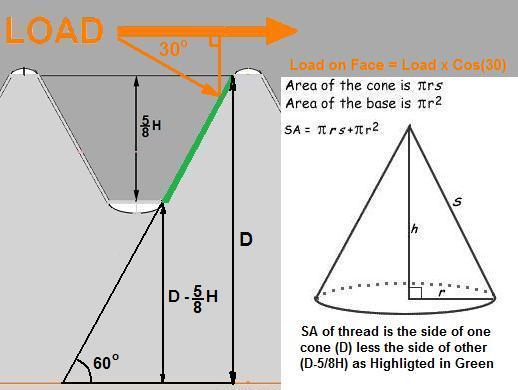
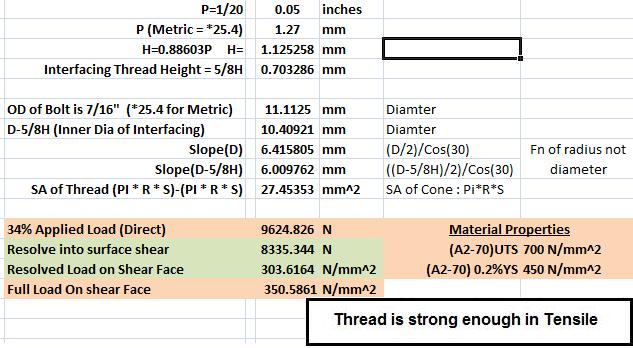
|
Conclusion On Theoretical Component
  |
Two independant theoretical calculation pathways have been used to demonstrate that an A2-70 graded Stainless Steel bolt is strong enough to be used for mounting seatbelts.
This succesful theortical outcome needs to be validated by hardware testing such that the US Federal Law used as the governing requirement can be satisified FULLY.
|
|